In industrial maintenance, big steel structures like ships and tanks have many problems. These include high-altitude risks, complex shapes, and low manual efficiency. Wall-climbing robots need to stick to and move on ship side walls. These walls can bend in various ways. They have rough surfaces, even when robots carry loads. When a robot sprays on a ship's surface, a reaction force occurs between them. The magnetic wheels need strong suction to manage this force. The WM series magnetic wheels from CCmagnetics provide a strong solution. Their permanent magnet technology boosts performance.
I. Magnetic Adsorption Technology: The Core Driving Force of Wall-Climbing Robots
(I) Comparison of Adsorption Methods and Advantages of Permanent Magnets
Wall-climbing robots use two primary adsorption methods: electromagnetic and permanent magnetic adsorption. Permanent magnetic adsorption is best for metal surfaces. Its strength is 3 to 5 times greater than that of other methods, and it handles wall defects better.
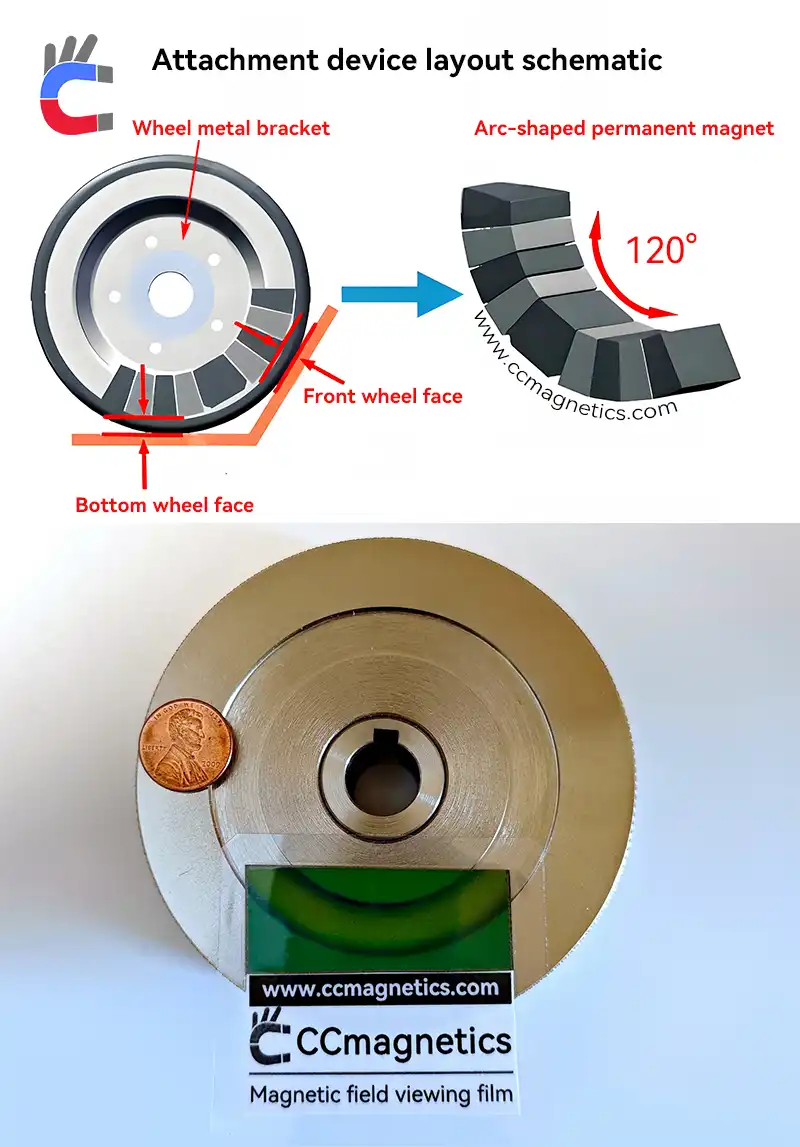
Electromagnetic vs. Permanent Magnet:
- Electromagnetic: Adjustable suction requires constant power. It risks falling if the power fails.
- Permanent Magnet (Core technology of WM series): It uses powerful neodymium iron boron magnets. This creates a strong, lasting force. The optimized magnetic pole layout balances distance and suction force. The distance ranges from 0 to 5 mm, while the suction force varies from 50 to 500 N per wheel. This design performs well on complex surfaces.
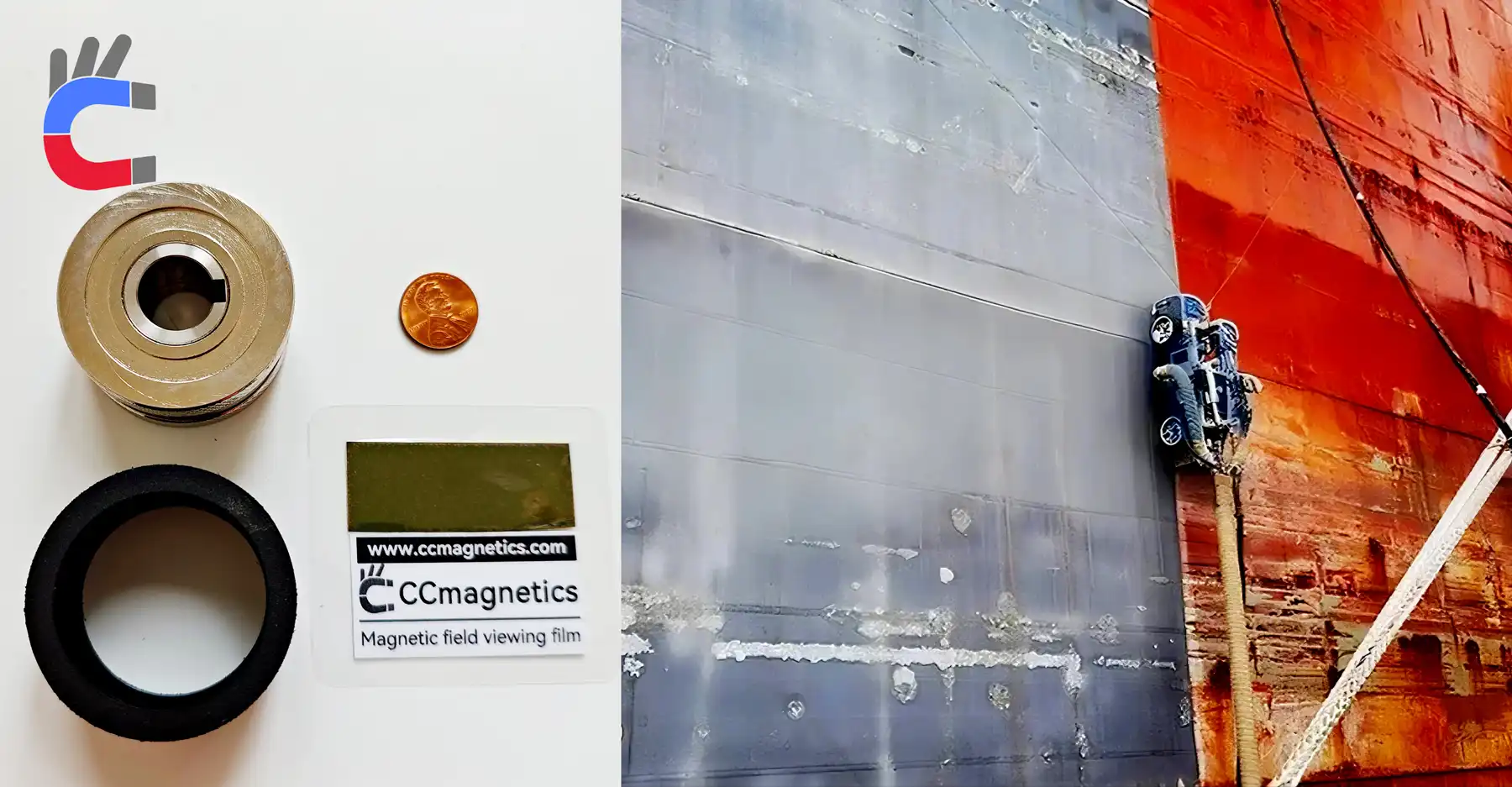
(II) Technical Parameters of WM Series Magnetic Wheels
- Dimensions: Outer diameter is from 40 to 180 mm. You can customize the width for different robot sizes.
- Load Capacity: Each wheel supports 5-150 kg, based on the model. It can handle heavy tools, like ultra-high-pressure water jets (280 MPa).
- Test Report: Contains data on suction force and impact resistance. It can withstand 2,800 bars of pressure for safe operations.
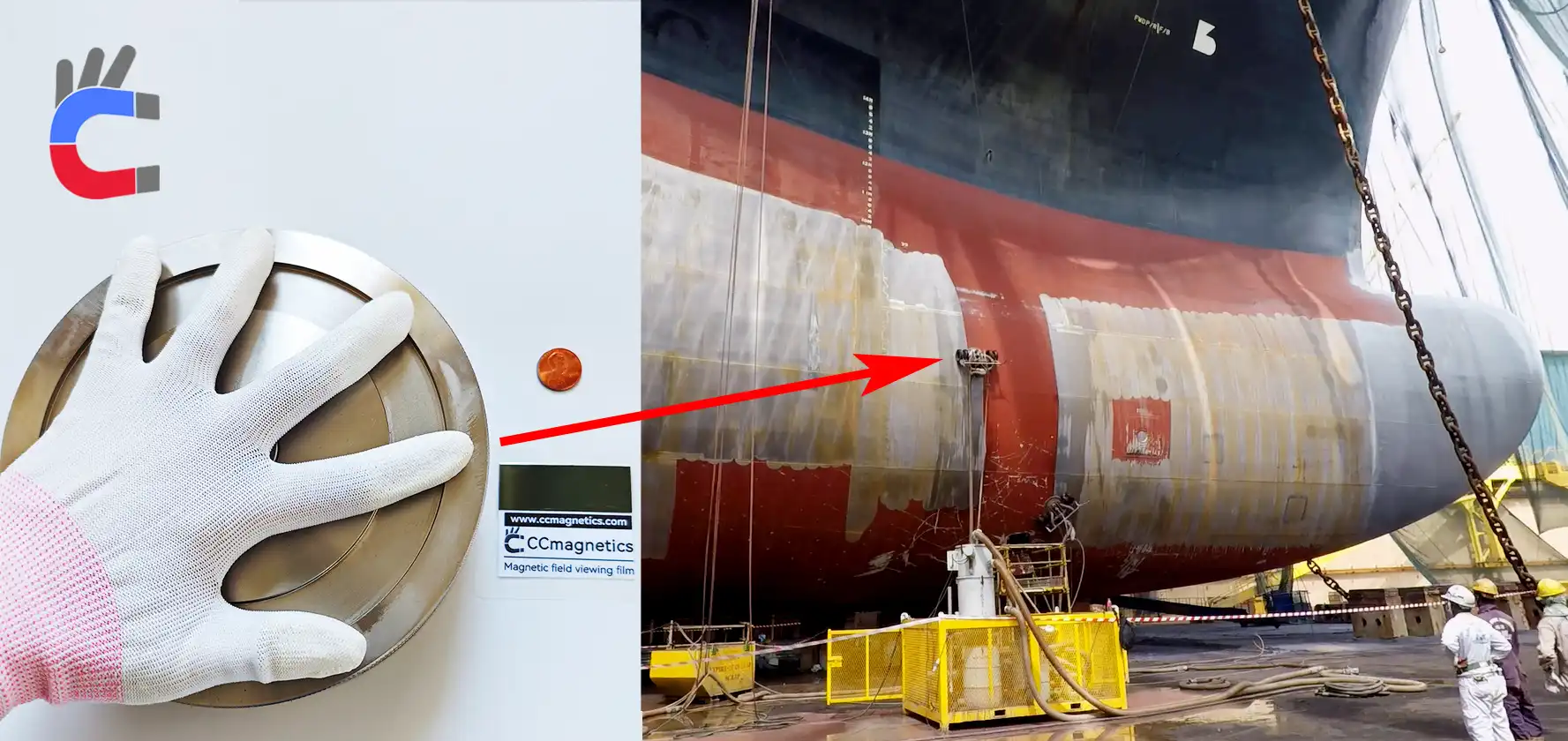
II. Typical Application Scenarios: Full Scenario Coverage from Storage Tanks to Ships
(I) Storage Tank Anti-Corrosion and Rust Removal: Solving "High-Altitude Operations" Challenges
-
Traditional Manual Pain Points:
- High risk of falls; dust and paint pose health hazards.
- Low efficiency (manual work on a thousand-square-meter tank takes weeks) and uneven treatment.
- Wastewater and waste residue harm the environment.
-
Intelligent Solution Driven by Magnetic Wheels:
- Integrated Design: The wheel chassis has permanent magnet wheels. This allows for 360° steering and helps it cross weld seams and uneven surfaces. It solves the steering and driving force issues faced by tracked robots.
- Ultra-High Pressure Rust Removal: This method achieves an efficiency of 60-90㎡/h. It reaches Sa2.5 grade and uses a vacuum recovery system for quick rust removal and drying. This ensures that the process recovers over 95% of wastewater.
- Painting operation: Spray gun width ranges from 300 to 1000 mm. It has an efficiency of 9 to 18 m²/min. The built-in gyroscope makes automatic corrections for better coating uniformity.
-
Working Condition Adaptation: From Storage Tanks to Complex Internal Environments:
- Outer Wall: It handles curvature with the smallest radius of 2 m. It also works well in extreme weather, staying stable in winds below level 6.
- Inner Wall: It’s remote-controlled. It crosses weld seams and water areas. This allows for unmanned grinding and painting. As a result, it cuts construction time by over 50%.
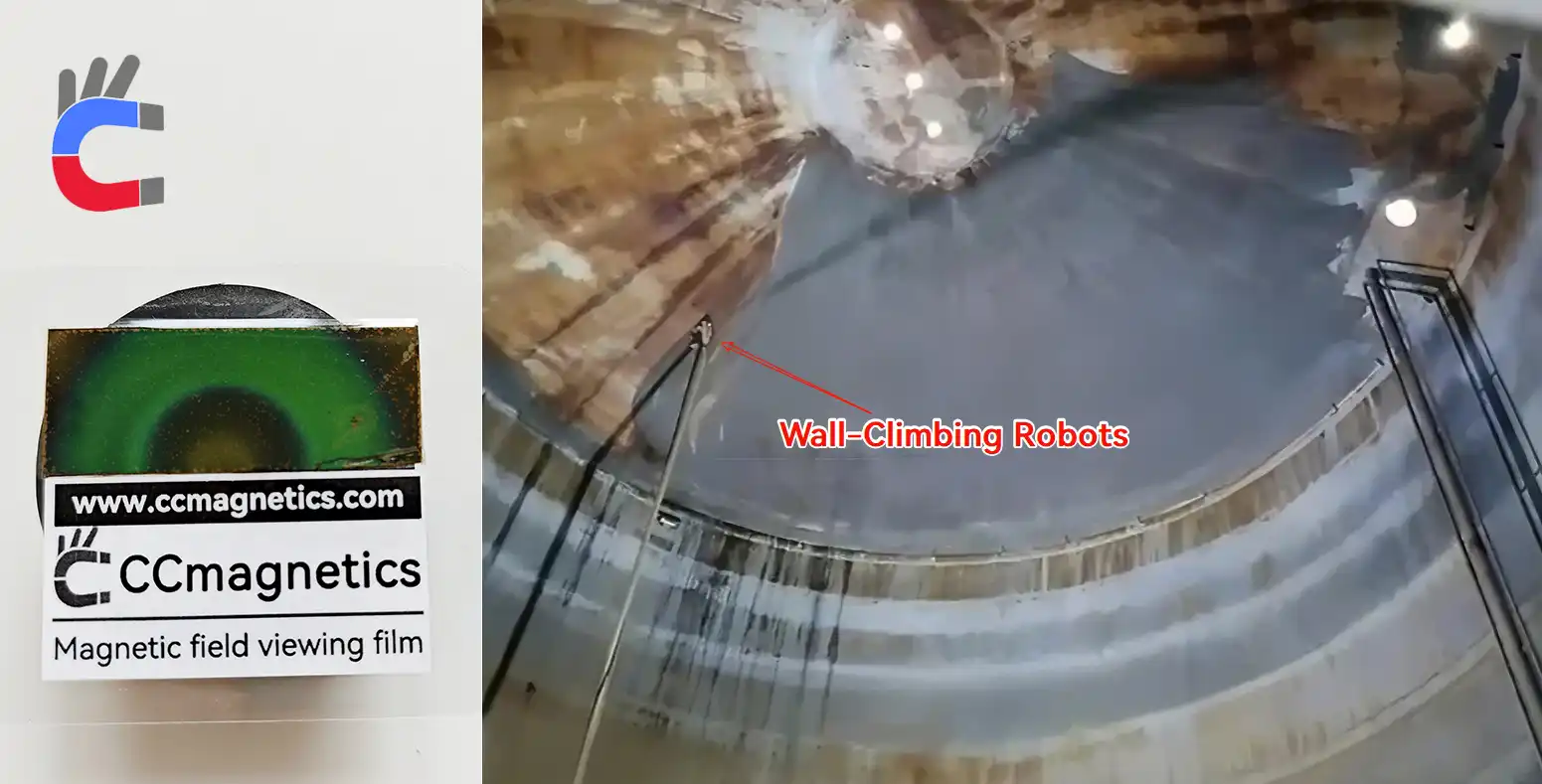
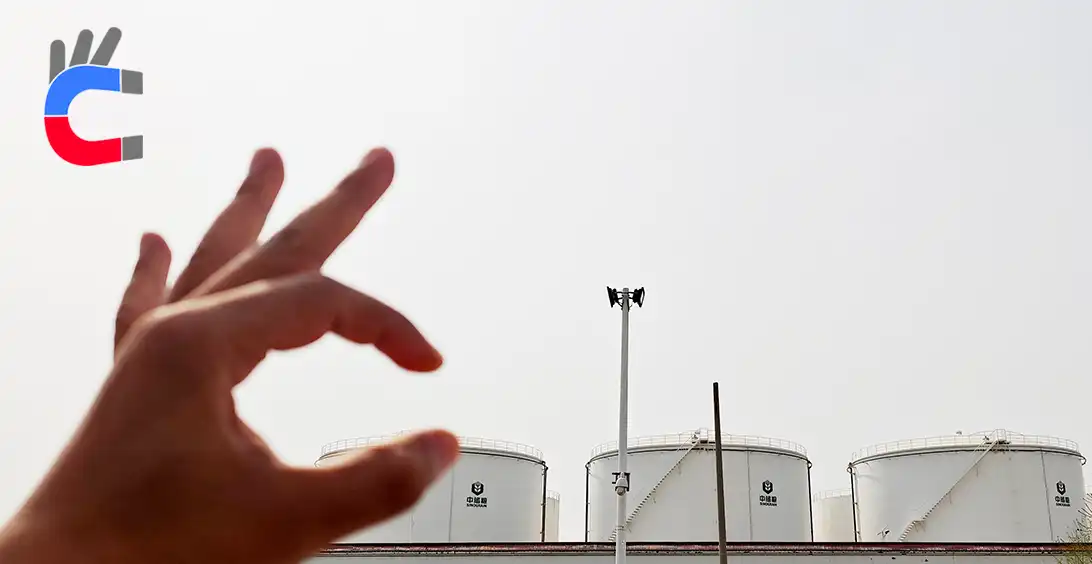
(II) Ship Hull Maintenance: Enhancing Environmental Protection and Efficiency
-
Magnetic wheel robots reduce dangers in manual operations. Traditional sandblasting causes dust pollution, while high-pressure water rust removal is an alternative. But, handheld spray guns face three main issues:
- Wastewater causes secondary pollution to the hull.
- Surface moisture leads to re-rusting, affecting coatings.
- High risks with operations above 230 MPa.
-
Technical Breakthroughs of Magnetic Wheel Robots:
- Load and Stability: It glides smoothly on curved ship surfaces, such as bulbous bows and superstructures. It works with an efficiency of 60-75 m²/h, matching the output of six manual workers.
- Quality Consistency: Mechanized operations stop errors and reduce corrosion from fatigue. This improves rust removal uniformity by 30%.
III. Summary of Core Advantages of Magnetic Adsorption Wall-Climbing Robots
Advantage Dimension
- Adsorption Stability: The force change rate for permanent magnet wheels is under 10%. In contrast, electromagnetic wheels exceed 30%. It supports stable adsorption with a 0-3 mm gap. This design eliminates slip-and-fall risks and adapts to defective walls.
- Movement Flexibility: Features a four-wheel-drive chassis with differential steering. The smallest turning radius is 200 mm, and it can cross obstacles up to 15 mm high. This allows it to navigate complex structures with ease.
- Load Capacity: Each robot can carry the largest load of 200 kg. It can use ultra-high-pressure pumps and recovery devices. This completes the whole process of "rust removal, recovery, and spraying."
- Environmental Adaptability: Operates in temperatures from -40℃ to 80℃. It has an IP68 rating and is resistant to salt spray, making it suitable for ships and offshore platforms. It performs well in extreme conditions, such as polar regions and high humidity.
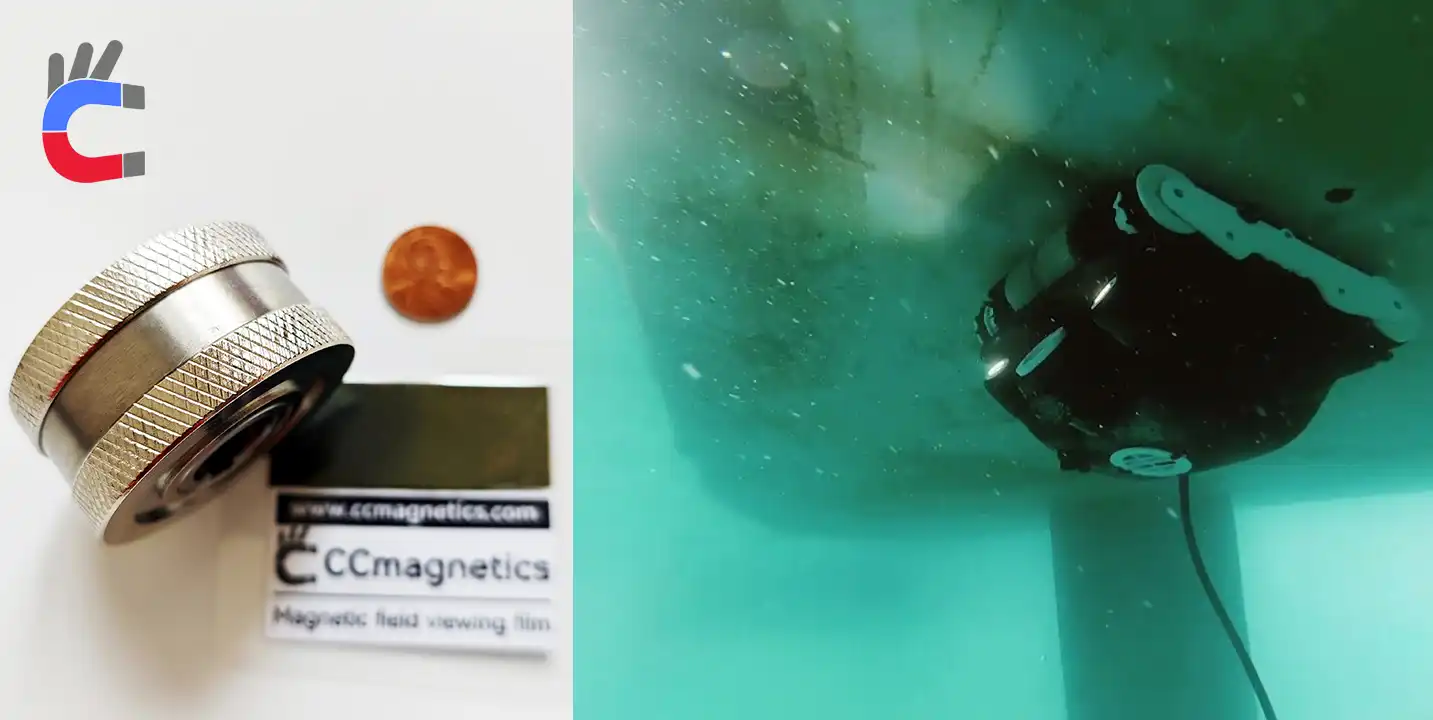
IV. Future Outlook: From "Replacing Manual Labor" to "Defining Standards"
Magnetic wall-climbing robots are now moving beyond storage tanks and ships. This change is part of the worldwide effort to save energy and protect the environment. They are now entering fields like nuclear power containment and bridge steel structures. CCmagnetics and similar companies face challenges like "adsorption, movement, and operation." They solve these issues with custom designs and creativity. This innovation creates new possibilities for working on complex surfaces.
For instance, CCmagnetics has introduced waterproof magnetic wheels. These are permanent wheels designed for cleaning the undersides of ships underwater. This reduces the cost of cleaning ships by a large amount. Small ships have needed divers for cleaning tasks throughout history. Workers clean large ships at the dock. Now, there are crawling robots with NdFeB permanent magnet wheels. These robots can clean ships underwater without rest. Magnetic wheels have challenges. One is how permanent magnets can stop slipping on algae. Another is whether special rubber tires will change underwater suction. CCmagnetics has conducted thorough exploration and found solutions to these problems.